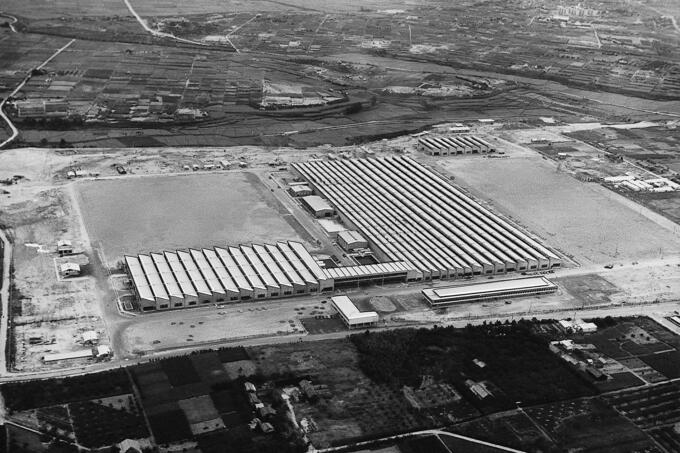
この記事をまとめると
■年間16万4000台のトヨタ車を世の中に送り出すトヨタ元町工場を見学
■製造途中の車両が組み立てライン上を自走する自走組み立てラインを開発中
■4万平方メートルのヤードでは10台のVLRロボットによる車両運搬を予定している
1959年に開業してトヨタの礎を築いた元町工場
トヨタ初の量産工場である元町工場の操業開始はなんと1959年である。ちなみにその名前の語源は「元・町工場」。トヨタにとっては、会社の発展の大きな礎となった工場なのだ。
元町工場での車両の生産台数は1990年にはじつに年間44万4560台に達したが、この20年ほどは一直、二直の繰り返しで、現在では16万4000台に落ち着いているという。改めて驚かされたのは、その内訳。ラインは現在、BEVやFCEV、HEV、そしてエンジン車の4つのパワーユニット、セダン、ミニバン、SUVという3つの車型の混流なのである。
ラインに流される順番は基本的には注文に基づくが、1台辺りの所要時間は、たとえばbZ4Xが8.8時間、MIRAIは11.3時間と異なる。bZ4Xのバッテリーのためには電池パックの組立工程が別に置かれ、MIRAIは高圧水素タンクの取り付け作業などが専用の組立工程で行なわれたあと、この混流生産ラインに入ってくる。工程辺りの作業時間には最大30秒の差があることから、混ぜ方は配慮されている。作業時間の長いクルマばかり連続して流れないようにするためだ。
こうした多品種のクルマを高品質で組み立てつつ、作業員の負荷を軽減するために、ラインにはさまざまな工夫が凝らされている。UM(Universal Modular)トレイは、アタッチメントの交換でさまざまなパワーユニットを搭載でき、同じ工程での車両への搭載を可能にする。
興味深いのは、これを含めて作業員の創意工夫によるカラクリ的なアイテムが多数使われていること。実際に作業する立場からのリアルなアイディアから生まれ、採用された作業補助アイテムは、延べ1500以上にもなるという。
そんな組み立てラインの景色も、近い将来にはまったく違ったものになっているかもしれない。トヨタは次世代BEVの導入を機に、工場生産ラインの大胆なまでの自動化を目指している。まさしく「工程2分の1」実現の重要なキーだが、それは同時に生産リードタイムも、さらには工場投資も2分の1にするという大革新である。
これを可能にするのが、車両への新モジュール構造の採用だ。次世代BEVは車体をフロント、センター、リヤの大きく3パートに分割する。フロントとリヤはギガキャストによる一体成型とされ、センターは床下にバッテリーを敷き詰めるかたちだ。
部品の組付けは各モジュールごとに行なわれる。たとえば現在は車両のなかに入り込んで行なっているインストゥルメントパネルやシートのなどの取付けを立ったまま作業できるようになる。作業員の負担が減るし、クオリティも高まる。作業時間の短縮はコスト削減に繋がるという具合である。
気になるのは分割して組み立てられたモジュールをどう結合するのか。ボルト留め、嵌合が主になるが、鉄とアルミの接合になる場合も考えられるため、さまざまな手段が検討されている。果たして、ボディ剛性がどうやって確保されるのかなど、クルマ好きとしては興味深いところだ。